Sono giunti al termine, lo scorso dicembre, i lavori di restauro e riqualificazione del principale teatro della città di Bergamo intitolato a Gaetano Donizetti, una struttura con oltre duecento anni di storia e con un volume molto importante che coinvolge visivamente sia la parte alta che la parte bassa della città.
La facciata storica è stata costruita con un calcestruzzo architettonico primordiale di inizio ‘900, gli elementi dei volumi laterali sono stati invece oggetto di interventi di ampliamento a cavallo tra gli anni ’70 e ’80 a opera dell’Architetto Pizzigoni attraverso l’impiego di un calcestruzzo di seconda generazione.
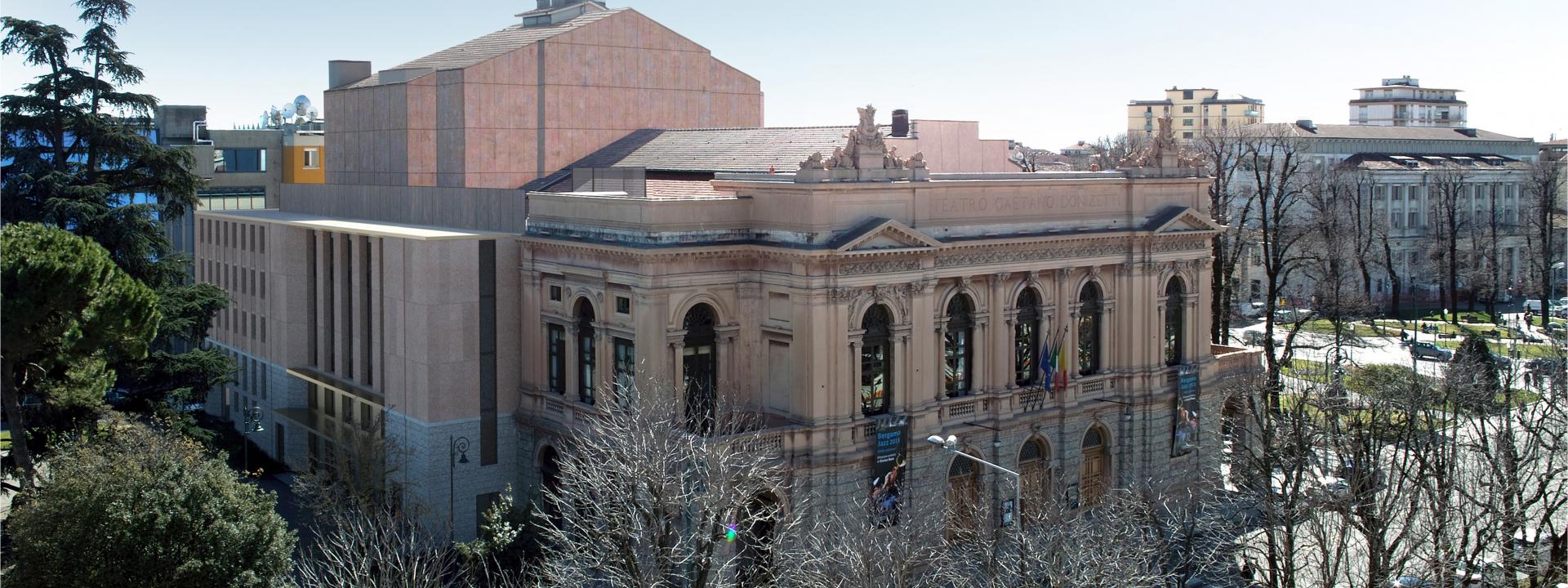
Oggi il Teatro Donizetti, a fronte delle opere di ristrutturazione e riqualificazione iniziate nel 2018, racconta una sorta di storia del calcestruzzo, un materiale molto caratterizzante per Bergamo, storicamente e culturalmente città di costruttori. La volontà di progettisti e architetti in accordo con la Sovrintendenza e la direzione artistica, è stata dunque quella di proseguire con l’utilizzo di un materiale cementizio evoluto al fine di rendere omogenea e contemporanea l’immagine architettonica del Teatro.
Il progetto, realizzato da Arassociati e dallo studio Berlucchi, prevedeva la riqualificazione dei volumi esterni e della torre scenica attraverso l’utilizzo di materiali che si inserissero in modo non invasivo in una struttura preesistente e che fossero espressione di innovazione e tecnologia, conservandone la facciata storica e le parti di pregio architettonico. A livello visivo, le facciate laterali e la torre scenica del Teatro Donizetti sono oggi un insieme di pannelli in calcestruzzo in differenti tonalità di rosa.
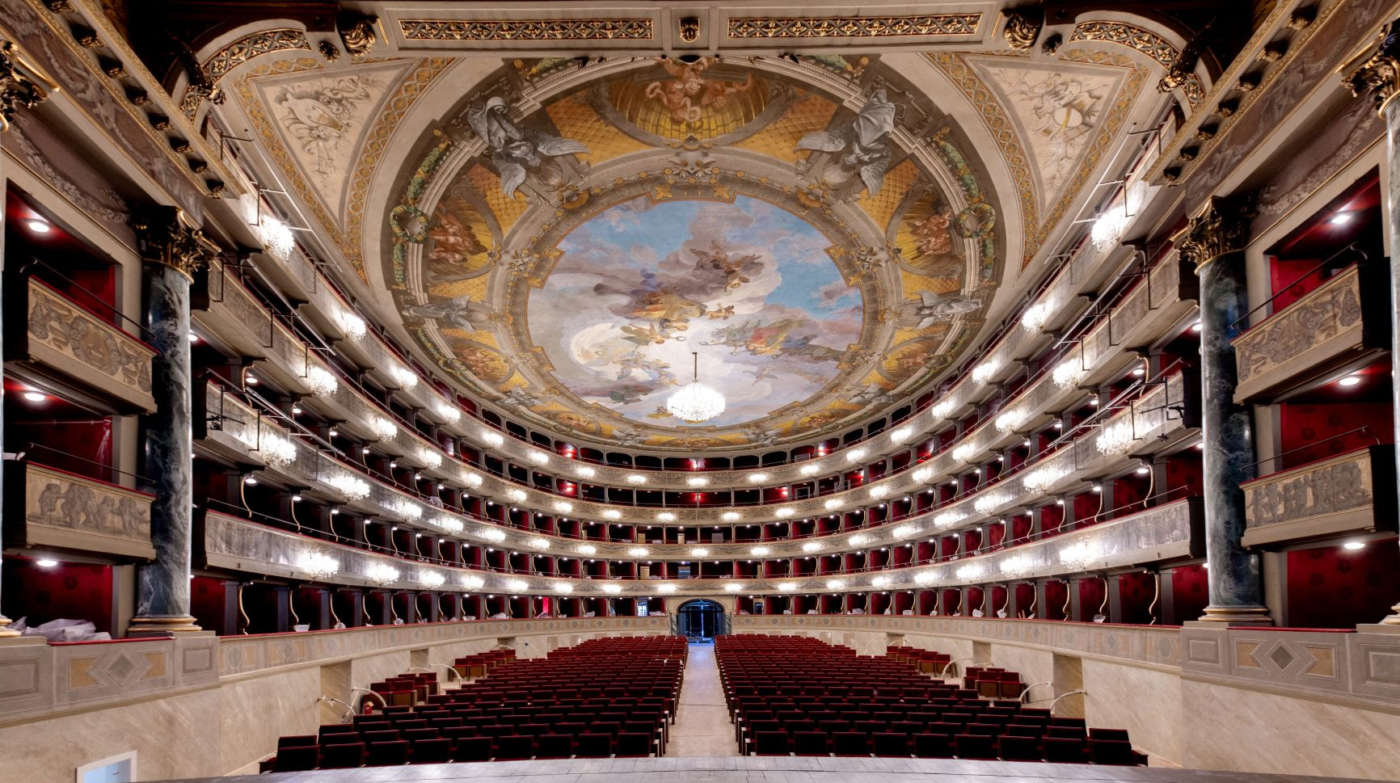
Magnetti Building si è occupata dello studio e dell’ingegnerizzazione dei pannelli di rivestimento, ma anche dei processi di installazione ed esecuzione dell’opera intervenendo sia su strutture esistenti che di nuova realizzazione. Si tratta di circa 800 lastre, elementi prevalentemente piani di grandi dimensioni ma di spessore ridotto, 3-4 cm. Alcune di queste sono state poi realizzate tridimensionalmente per la riproduzione delle lesene verticali sul prospetto laterale dei camerini e degli ambienti polivalenti.
Il materiale utilizzato è la malta Effix prodotta da Italcementi, che presenta elevate prestazioni meccaniche e un’alta durabilità grazie al suo mix design. Le lastre sono rinforzate internamente da una rete in fibra di vetro, applicata sui punti di sospensione e ancoraggio, che garantisce un comportamento post fessurativo parzialmente duttile e sicurezza al prodotto in caso di danneggiamento.
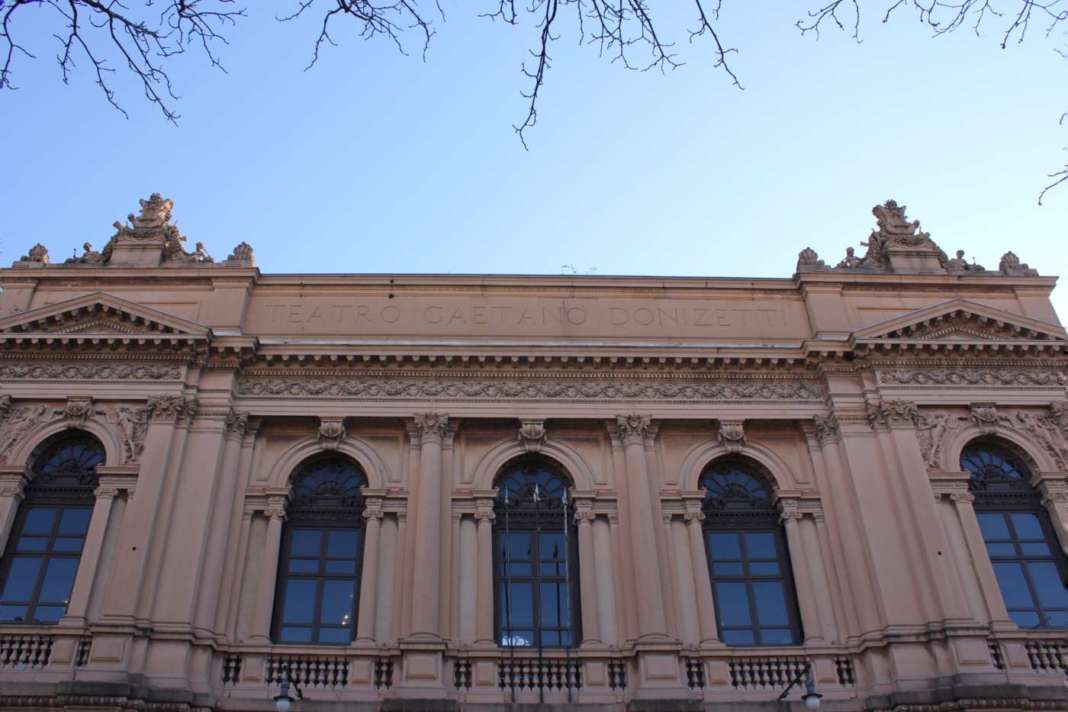
Partendo da un’indagine colorimetrica del Teatro al fine di ricercare delle tonalità che si avvicinassero il più possibile alle colorazioni presenti su tutta la struttura esistente e attraverso il dosaggio di ossidi all’interno della malta, sono state selezionate le cinque gradazioni di rosa e giallo più idonee ad armonizzarsi con il volume.
Dopo un lungo percorso di qualche centinaio di campioni e dopo aver sondato diversi livelli di finitura tramite trattamenti superficiali di varia natura, è stato raggiunto il livello desiderato dalla direzione artistica e dalla Sovrintendenza con un trattamento di microsabbiatura, protetta da uno strato idrorepellente. Una finitura volutamente non liscia che dona al Teatro un effetto antico e moderno allo stesso tempo.
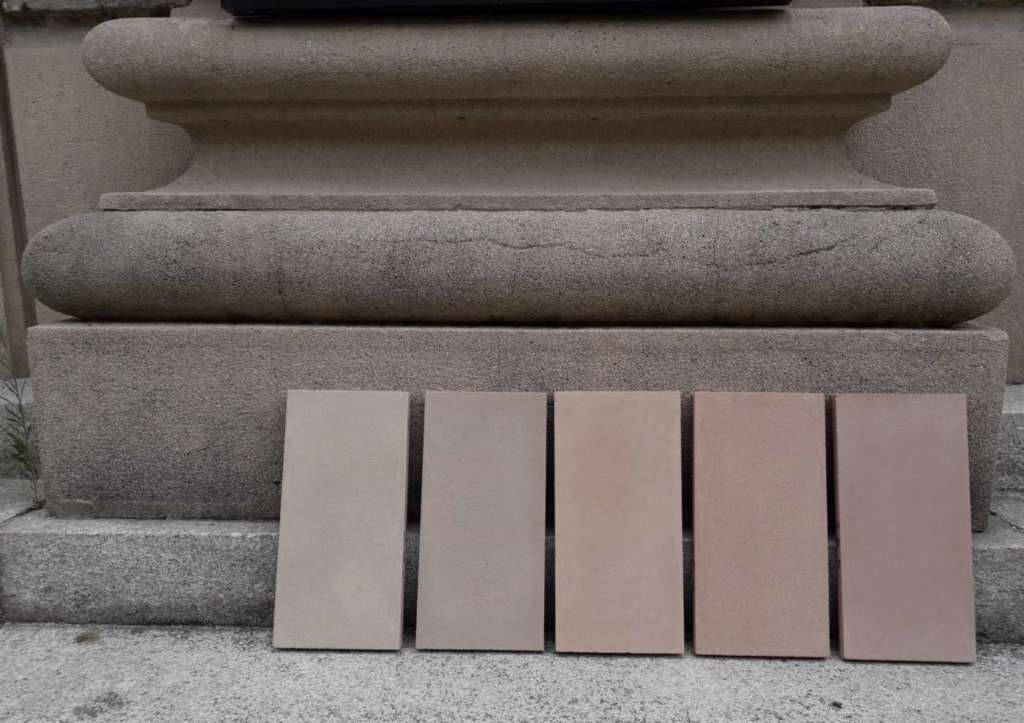
L’esperienza di Magnetti Building nel campo della prefabbricazione ha consentito di individuare sistemi di installazione inseriti già nella fase di produzione e dotati di un sistema di microregolazione per la messa in planarità delle lastre durante il montaggio, realizzati nello stabilimento di Carvico.
Complice lo stop forzato a causa della pandemia, la produzione delle lastre ha attraversato più stagioni, esponendo il materiale a differenti condizioni ambientali nella fase più delicata della sua maturazione. Al fine di prevenire fenomeni di fessurazione nelle ore successive alle operazioni di getto della malta, nel reparto produttivo di Magnetti Building sono stati adottati speciali accorgimenti e attrezzamenti per attuare la maturazione umida delle lastre tramite immersione in acqua.
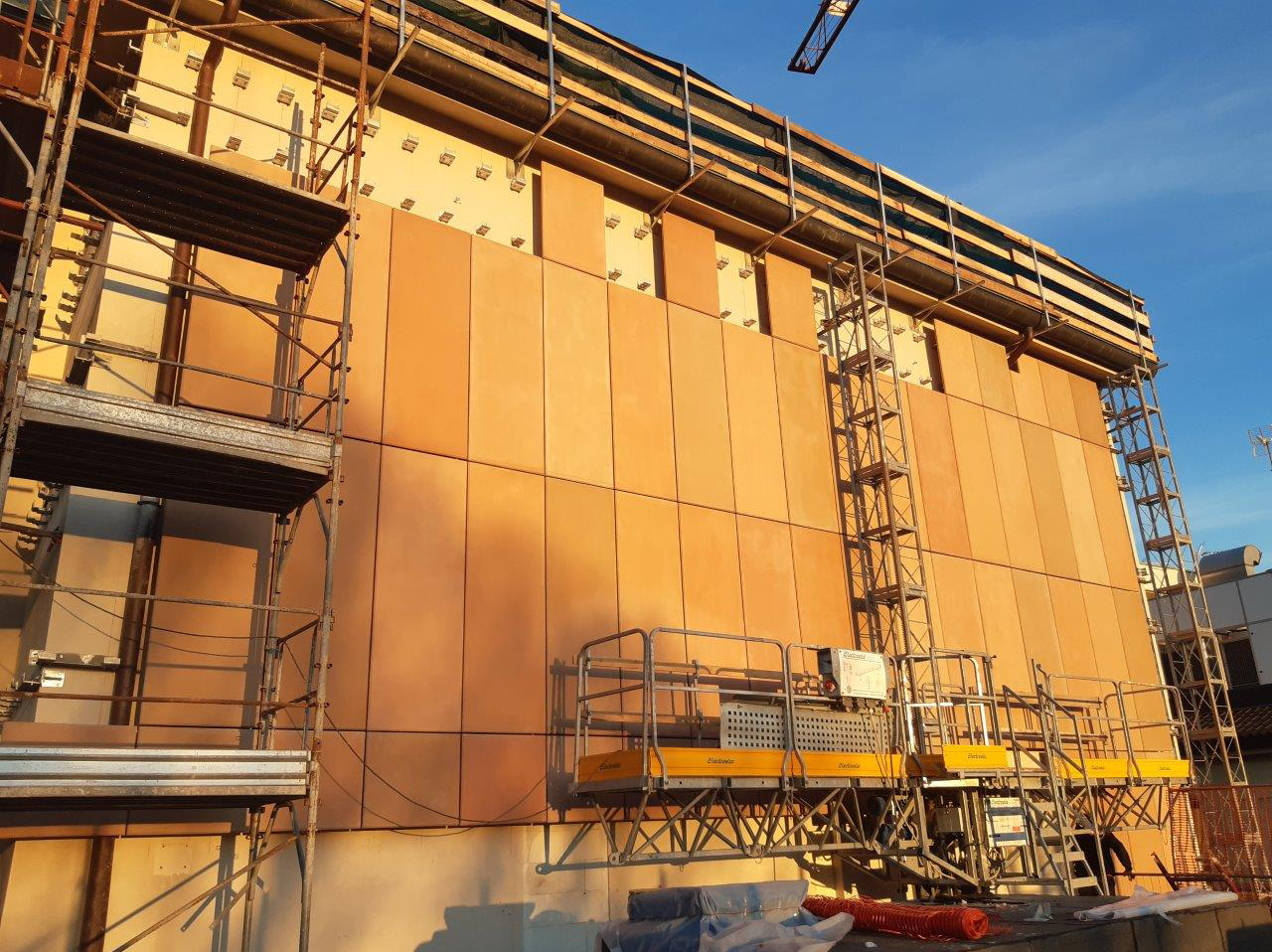
In parallelo all’attività di ingegnerizzazione e produzione, il materiale e il prodotto finale sono stati validati con test eseguiti presso il Politecnico di Milano. In particolare, la conformità delle lastre ai requisiti richiesti dalla destinazione di installazione è stata ottenuta con prove di urto da corpo molle e corpo rigido, secondo standard internazionali.
Un progetto ambizioso studiato ad hoc nel quale Magnetti Building si è dimostrata capace di modificare e adattare i propri processi e i propri standard produttivi in relazione alle richieste di una realizzazione particolarmente esigente dal punto di vista cantieristico e di progettazione. (vb)