A volte le maggiori difficoltà si nascondono dietro a un aspetto di facciata lineare, regolare, fin quasi rassicurante: in realtà, spesso le apparenze ci possono ingannare. È proprio nell’apparente semplicità che risiedono le complessità più nascoste, che necessitano di risposte mirate, studiate su misura.
Ecco allora che di fronte a una costruzione monolitica come un nuovo mulino per lo stoccaggio di farine vegetali realizzato nei pressi di Modena, ci sentiremmo di primo acchito di non preoccuparci troppo, pensando a un enorme parallelepipedo di calcestruzzo che tutto sembra tranne che una costruzione complessa.
Dietro a questa prima impressione si cela invece un processo costruttivo che è stato oltremodo stimolante e impegnativo per i soggetti che vi hanno preso parte, soprattutto nel soddisfare le esigenze di un ciclo produttivo che è composto da numerosi passaggi, a ognuno dei quali corrisponde una serie di contraltari costruttivi decisamente non convenzionali.
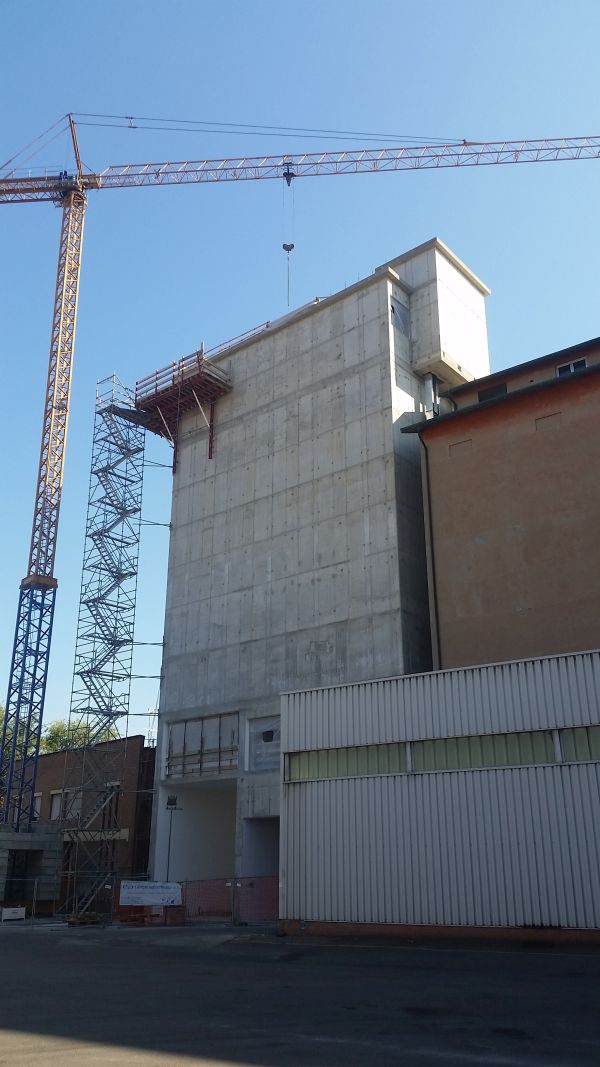
Trattandosi di una sorta di monolite in calcestruzzo, l’aspetto di maggior interesse è certamente rappresentato dall’attrezzatura con cui si modella a piacimento tale materiale: le casseforme, in tutte le loro variabili.
Un ruolo dunque determinante nel cantiere ha avuto Alsina, società iberica produttrice di sistemi di casseforme integrati, che ha operato in maniera diretta come sostegno e sviluppo tecnico per l’impresa esecutrice.
È sufficiente analizzare una sezione tipo del nuovo edificio per rendersi conto dei numerosi salti di quota, ambienti a doppia altezza, sbalzi, che caratterizzano l’anima del manufatto, problematiche che hanno necessitato dello studio di soluzioni tecniche studiate «ad hoc».
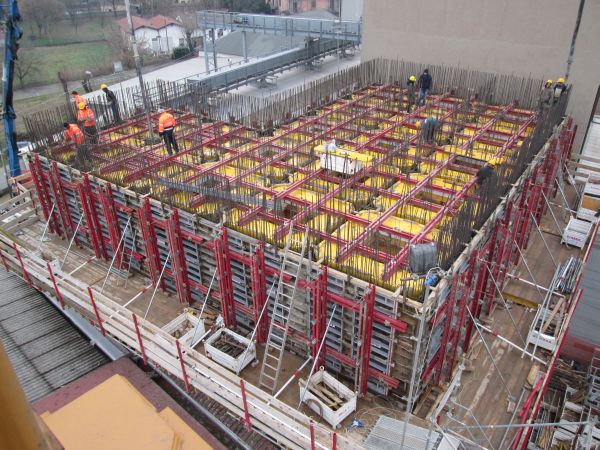
L’edificio è infatti composto da un primo livello a quota terreno all’interno del quale avvengono le operazioni di carico delle farine sugli autocarri destinati a tale scopo ed ha un’altezza netta di oltre 7 metri. Salendo troviamo poi un piano tecnico all’interno del quale sono alloggiati i macchinari che permettono il funzionamento dell’intero presidio, al di sopra del quale risiede il vero e proprio cuore del mulino: l’area delle tramogge, che rappresentano il filtro di stoccaggio e carico delle farine. Dall’area tramogge si innalzano per oltre 15 metri ben 19 silos di stoccaggio fino alla sommità dove vi è infine un ulteriore piano, con un corpo a sbalzo verso l’esterno.
Entrando nel dettaglio, sono sostanzialmente tre le fasi di cantieristica che hanno suscitato il nostro maggior interesse; le analizziamo di seguito.
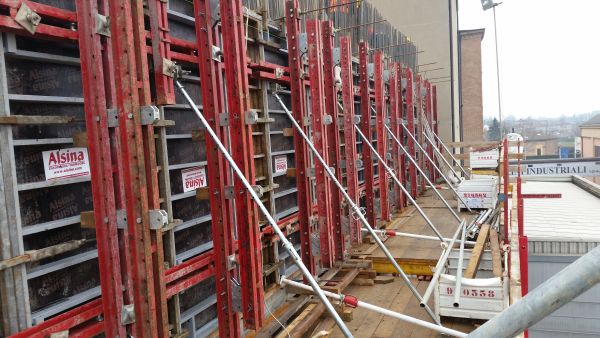
La realizzazione delle tramogge di carico è certamente la parte più affascinante dal punto di vista costruttivo: si tratta di un’operazione poco convenzionale e che ha impegnato i tecnici di Alsina e l’impresa esecutrice (Lavori Industriali srl) al fine di trovare le soluzioni esecutive più idonee.
Come visibile dalle immagini l’obiettivo era la costruzione di 19 silos di stoccaggio e carico farine, dalla conformazione troncoconica rovescia: la zona di alloggiamento ha un’altezza utile netta di 3 m ed è stata concepita come un monoblocco in c.a. al fine di garantire una perfetta aderenza e continuità con le pareti perimetrali e intermedie.
Lo stoccaggio di farine, infatti, nasconde delle insidie non note ai più e in particolar modo l’alto di livello di esplosività quando in presenza di grossi quantitativi, nonché l’assoluta necessità di avere una superficie interna dei bacini di stoccaggio il più possibile liscia e priva di asperità, pena la creazione di blocchi interni «ad arco», con conseguente impossibilità di far confluire il contenuto dei silos verso la zona inferiore della struttura, e la creazione di ristagni di polveri, causa di una scarsa igienicità dell’ambiente.
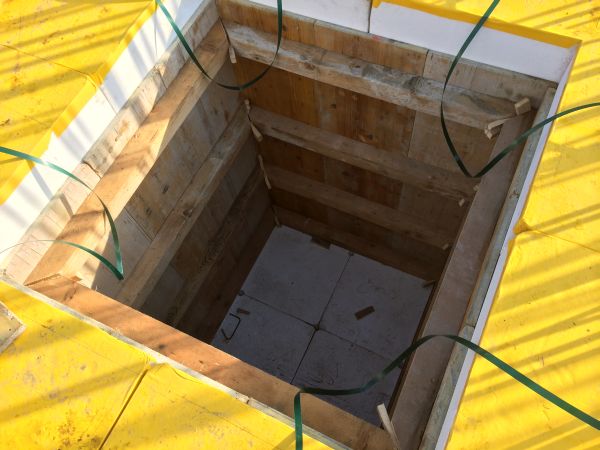
La forma troncoconica rovescia è stata ottenuta realizzando 19 elementi negativi in polistirene ad alta densità, che sono stati inseriti in appositi collari all’uso predisposti, annegati nella soletta in c.a. di appoggio; ogni tramoggia, la cui dimensione finale è di 2,95×2,95×3,25 mt (b x l x h) è stata scomposta in quattro parti, per renderne possibile il trasporto.
Particolare interessante, i negativi in polistirene sono stati concepiti a una doppia densità, maggiore mano a mano che ci si avvicina alla sezione più stretta del cono, questo perché la forza di spinta generata dal calcestruzzo in opera durante le fasi di getto era veramente considerevole; per lo stesso motivo, nella parte centrale di ogni negativo è stata predisposta una centinatura lignea al fine di aumentare la resistenza e diminuire le deformazioni relative derivanti dalla pressione del getto.
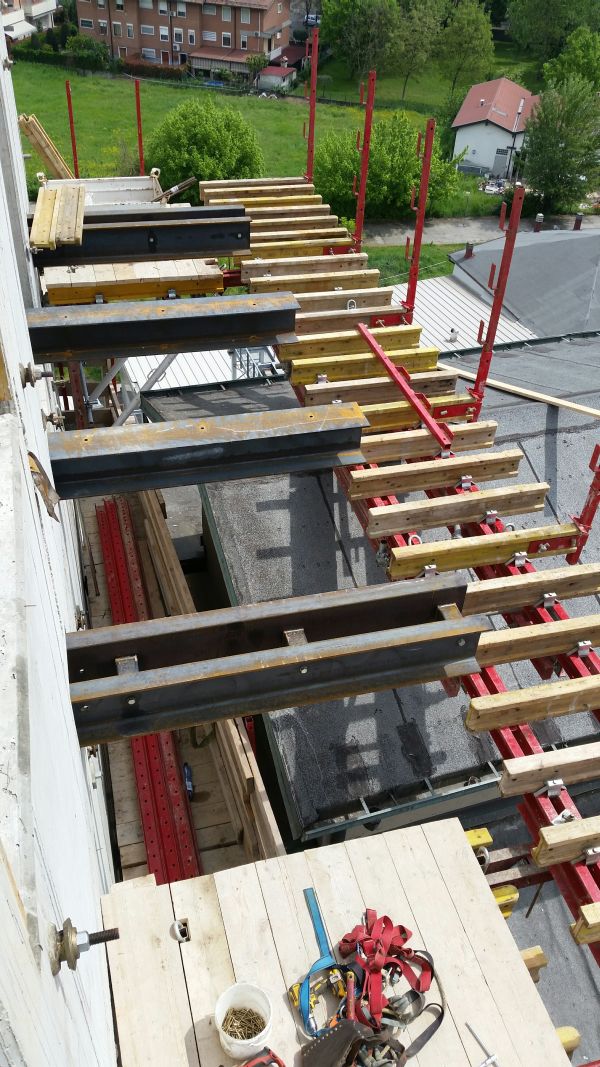
Per la casseratura esterna delle pareti delle tramogge, invece, è stato utilizzato il sistema Rampante Multiform Alsina, composto da pannelli metallici di spessore 15 cm alti 3,00 m del sistema Alsina Alisply Retto, con pressione di esercizio pari a 60 kN/mq.
Altro particolare rilevante, per garantire la tenuta stagna del monoblocco, non sono state usate le classiche barre Dywidag passanti ma un triplo sistema di tirantaggio, diversificato tra parte inferiore, parte superiore e parte centrale:
– parte inferiore: barre Dywidag collegate tramite tiranti annegati nel calcestruzzo alla soletta di appoggio;
– parte superiore: sistema reticolare formato da travi metalliche Alsina Multiform 2 Upn e barre Dywidag che collegano i lati opposti dell’edificio.
– parte centrale: per contrastare gli effetti di galleggiamento delle tramogge durante la fase di getto dovuti alla Spinta di Archimede, è stato predisposto un ulteriore sistema di barre Dywidag verticali collegando il reticolo di travi superiore a travi di contrasto posizionate all’intradosso della soletta di appoggio.
Insomma, un’operazione oltremodo complessa e impegnativa anche per la quantità di materiale gettato in opera, pari a circa 280 mc di calcestruzzo, opportunamente puntellati con sistemi di sostegno modulari.
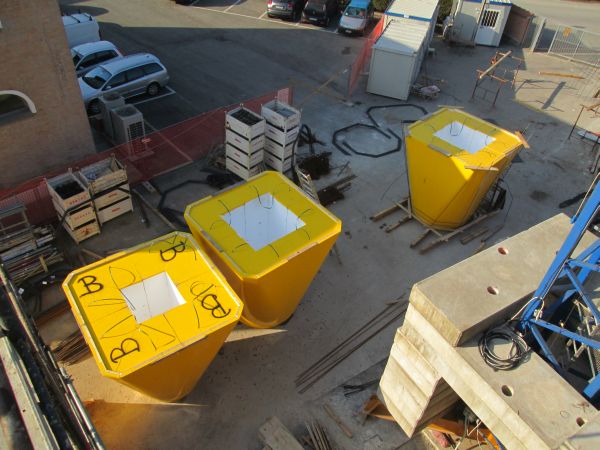
Proprio la metodologia di sostegno dei solai di copertura è il secondo aspetto del cantiere che vale la pena di analizzare con maggior attenzione. La copertura dei 19 silos consiste in una soletta piena in cemento armato dello spessore di circa 25 cm, posta a oltre 27 metri di quota dal piano strada e con un’altezza netta interna di interpiano di 16,50 m.
Appaiono fin da subito evidenti, quindi, le difficoltà che si sono dovute affrontare per operare una puntellazione in sicurezza con un’altezza così importante: l’ufficio tecnico Alsina, intervenuto direttamente nello sviluppo e nell’assistenza di cantiere, ha studiato un sistema di casseratura «aggrappato» alle pareti dei silos, sfruttando come piano di lavoro sicuro quello offerto dal sistema rampante interno montato in precedenza. Il tutto è stato corredato da scale e accessi di sicurezza, costituiti da elementi del Sistema Multidirezionale Alsina che l’Azienda spagnola ha messo a disposizione.
Un ultimo particolare è dato dal corpo a sbalzo presente in corrispondenza dell’ultimo piano di calpestio dell’edificio: su questo particolare, apparentemente secondario data la mole del manufatto complessivo, si è però concentrata una notevole applicazione tecnica studiata «ad hoc».
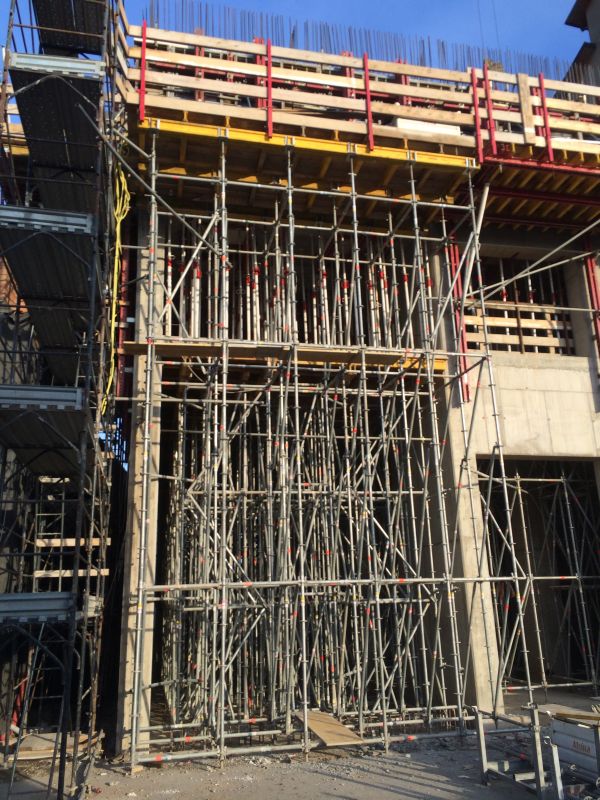
Le criticità, infatti, erano rappresentate dalla notevole vicinanza del vecchio mulino esistente, a meno di un metro da quello nuovo e dall’altezza da terra dell’intradosso del solaio di pavimento, superiore ai 20 metri.
Per evitare delle casserature a perdere peraltro abbastanza improbabili nella messa in opera, si è optato per la formazione di un «tavolo di casseratura» (per il getto della soletta) appeso tramite barre Dywidag a dei profili in acciaio (Hea 300 e 2 Upn 320), a loro volta fissati alla soletta interna del mulino e posizionati a sbalzo rispetto alla facciata dell’edificio; le superfici di lavoro sono state realizzate con Rampanti Multiform in posizione laterale, frontale e sottostante rispetto alla soletta da gettare.
Un’operazione certamente non agevole, data la quota dei piani di lavoro e la ristrettezza degli spazi in cui si è dovuto lavorare.
La realtà Alsina in Italia. La filiale italiana di Alsina è presente dal 2007 con sede ad Agrate Brianza (MB), dove risiedono gli uffici commerciali e il magazzino. La lunga esperienza nel campo dell’edilizia residenziale e civile ha permesso di sviluppare diversi prodotti che si sono adattati perfettamente al mercato italiano, consentendo di penetrare in maniera veloce e progressiva il mercato lombardo e del nord Italia. L’ulteriore sviluppo e investimento del Gruppo Alsina in prodotti studiati per le infrastrutture sta ultimamente permettendo anche alla filiale italiana di poter entrare in questo tipo di mercato, arricchendo e completando così a 360 gradi il proprio curriculum di cantieri. L’obbiettivo per i prossimi anni, avendo fiducia in una ripresa generale del mercato italiano delle costruzioni, è quello di consolidare la propria presenza su tutto il territorio nazionale, e di incrementare il business delle vendite dedicate ai grandi cantieri all’estero, mantenendo comunque la propria vocazione e specializzazione nel servizio di noleggio diretto.
IL CANTIERE
Impresa esecutrice: Lavori Industriali srl
Committente: Molini Industriali spa
Dislocazione cantiere: Modena
Durata: 6 mesi (2014-2015)
Sistemi di casseratura: Alsina spa – Agrate Brianza (Mb)
Responsabili Alsina: ing. Ivano Belli (Responsabile tecnico), ing. Nicola Lauria (Tecnico-commerciale), ing. Francesco Tardini (Responsabile commerciale)
Dati quantitativi
Opere di sottofondazione: Diaframmi profondità 25m – circa 1250 mc di Cls e circa 198 Ton di ferro per C.a. preassemblato in gabbie;
Platea di fondazione: 230mc di Cls e 34 Ton di ferro per C.a.;
Struttura di elevazione: 1480 mc di Cls e 250 Ton di ferro per C.a.
Materiale Alsina: 860 mq di pannelli metallici, per un totale di 185 ton di materiale consegnato
Sistemi utilizzati: Impalcatura Multidirezionale Cl-40, Alumecano, Rampante Multiform, Alsiply Muri, Rampante Interno, Scala di accesso.
Scarica il pdf della sezione verticale esplicativa dei vari livelli del mulino >>